Image Credit : Studio Bark
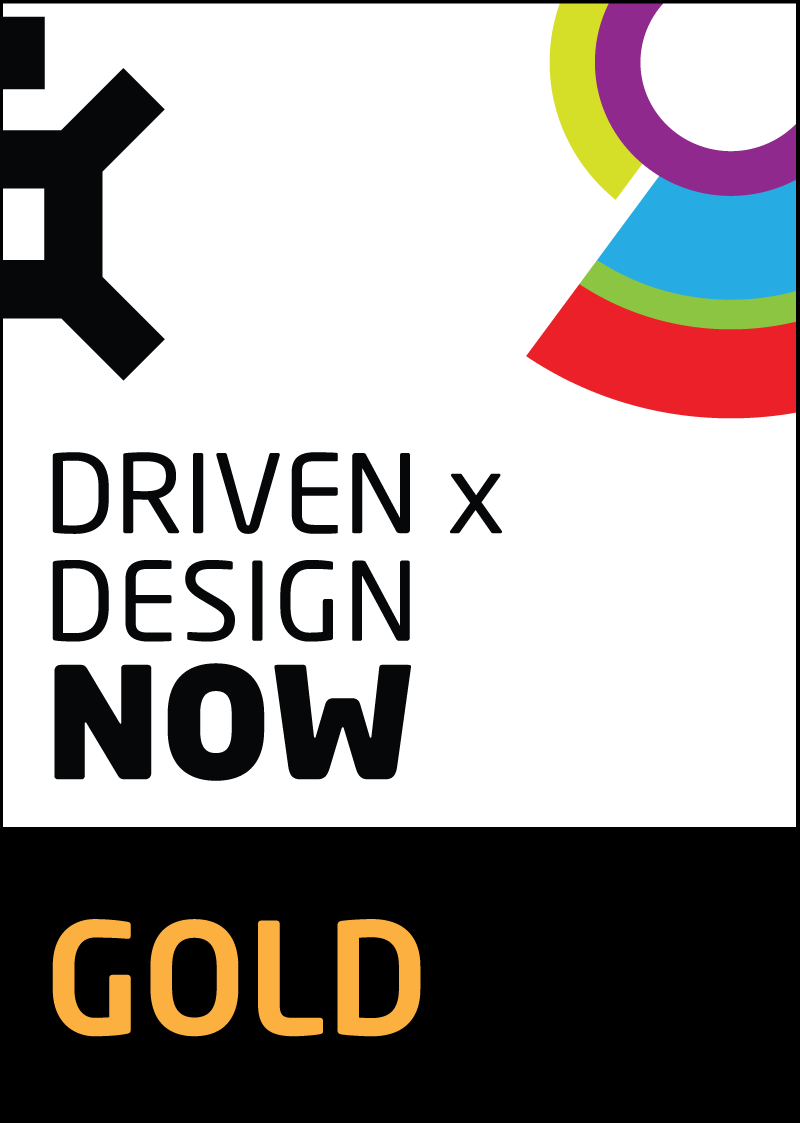
Project Overview
The Box House is a pioneering prefab project constructed using Studio Bark’s innovative U-Build construction method - a revolutionary modular self-build system.
Project Commissioner
Project Creator
Project Context
The scheme is one of 10 pilot houses, built side by side as the first street in Graven Hill, Bicester: a pioneering development of 1900 Custom and Self Build houses (CSH). The Graven Hill project is of national significance, a ‘vanguard’ project aiming to help the government double the CSH market by 2020.
The clients wanted to be involved in the construction of their house and were interested in the benefits associated with prefabricated (off-site) housing. However, they did not have the budget to pay for an external contractor, nor the specialist skills to lead the build process themselves.
In response to this challenging brief, Studio Bark developed an innovative system of CNC cut timber building blocks. Later coined as U-Build, the system is designed to provide a robust and affordable self-build solution for keen self-builders with limited construction experience.
Project Innovation
U-Build offers a hybrid offsite solution which removes many of the difficulties associated with traditional construction. The system harnesses the accuracy, speed and repeatability of offsite manufacture. It was developed with structural engineers Structure Workshop and prototyping / manufacturing from Cut and Construct.
The spruce plywood shell and core of the 2 bedroom, 90 sqm prototype house took just 4 weeks to construct. This was done by the client and a small team of architecture students, with the assistance of Studio Bark Projects. In the following 8 weeks the internal fit-out (kitchen, stair and internal partitions) was completed by Studio Bark Projects. While this was happening, other trade contractors installed mechanical and electrical services and the green roof.
Box House was constructed over the course of summer 2017 by the client and a small group of architecture students, as part of Studio Bark’s annual Bark Live Build.
Bark Live Build seeks to bridge the gap between architectural education and the on-site application of architecture. Architecture students can graduate from university with very little understanding of materials, construction terminology, or technical detailing. The construction of Box House as a student build project enabled Studio Bark to pass on these practical and professional skills. During the project, the brilliant student team lived ‘off-grid’ in a temporary campsite nearby made from reclaimed materials and including a luxurious composting toilet, a covered dining area and a hot shower.
The self-build portal suggests that it takes 6-9 months to construct a residential house. The Box House showed that an equivalent U-Build house can be delivered in 4 months.
Sustainability
Studio Bark reduced the whole life costs through a robust ‘fabric first’ approach including high-levels of insulation and inherent airtightness. In the future, self-builders can replace the parts at minimal cost, and remove individual panels to access services for maintenance.
All windows of the house were triple glazed. U-values were at passivhaus levels 0.15 Wm2K and airtightness is also predicted to be at passivhaus levels. The house benefits from a green roof and 2kWp solar panel system.
The insulation is so effective that the building does not need radiators; a single loop of 22mm copper pipe is sufficient to provide background warmth, saving cost, materials and maintenance. Further, the copper pipe was surface-mounted, providing a design feature that did not intrude upon the finished positions of furniture.
Environmental consultants Atmos Lab conducted a study. It concluded that the embodied carbon for a U-Build house would be circa 238 kgCO2/m2 as compared to 550 kgCO2/m2 for an equivalent house built with traditional construction methods.
The supply chain uses materials with environmental certifications. This including FSC and PEFC, such as Riga Birch plywood and WISA spruce plywood. Other non-toxic, ecological materials are specified including sheep’s wool insulation.
Commercial - Space
Commercial projects recognises that design is the means to create meaningful experiences for users, create value for people and drive profit for businesses.
The space category celebrates the design process and outcomes of planning, designing and constructing form, space and ambience that reflect functional, technical, social, and aesthetic considerations. It includes architecture, interior design and landscape design as well as set display and exhibition design.
More Details